Workshop services:

Degreasing, pickling, passivation, descaling, chemical polishing and electropolishing of major metals are daily and perfectly controlled operations. Chimideruil stands out among other things by its speed of execution linked to an impeccable quality of finish. This equation is made possible by a perfectly adapted product development capacity and regulary analyzed treatment baths.
In order to best meet the needs of our customers, is our workshop in Ghlin equipped with baths for the following treatments:
Pickling and Passivation

Pickling stainless steel consists of dissolving the mixed oxide layer formed during the welding process. This mixed oxide layer has a chromium content that is too low to allow the development of the passive layer specific to the “stainless” character of these steels.
Once this layer has been removed, the chromium present can oxidize on contact with air or water and form a continuous film: this is what we call the passivation phenomenon.
This passivation can either be formed “naturally”, upon contact with ambient air, or be accelerated by the chemical action of an oxidizing agent.
- Par circulation
- Par pulvérisation
- Par immersion
- By circulation
- By spraying
- By immersion
Before
After
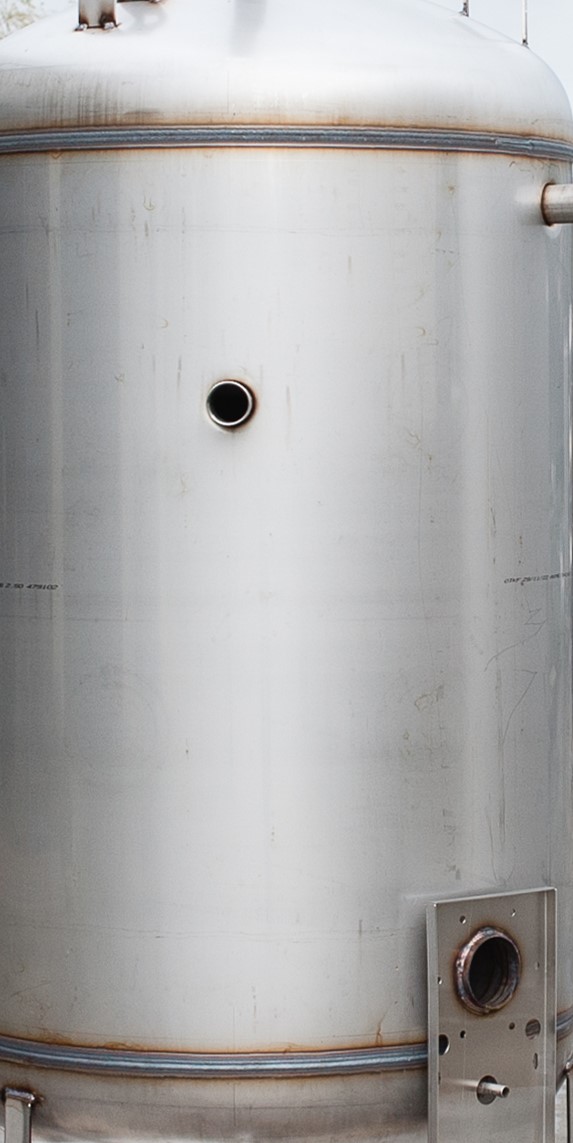
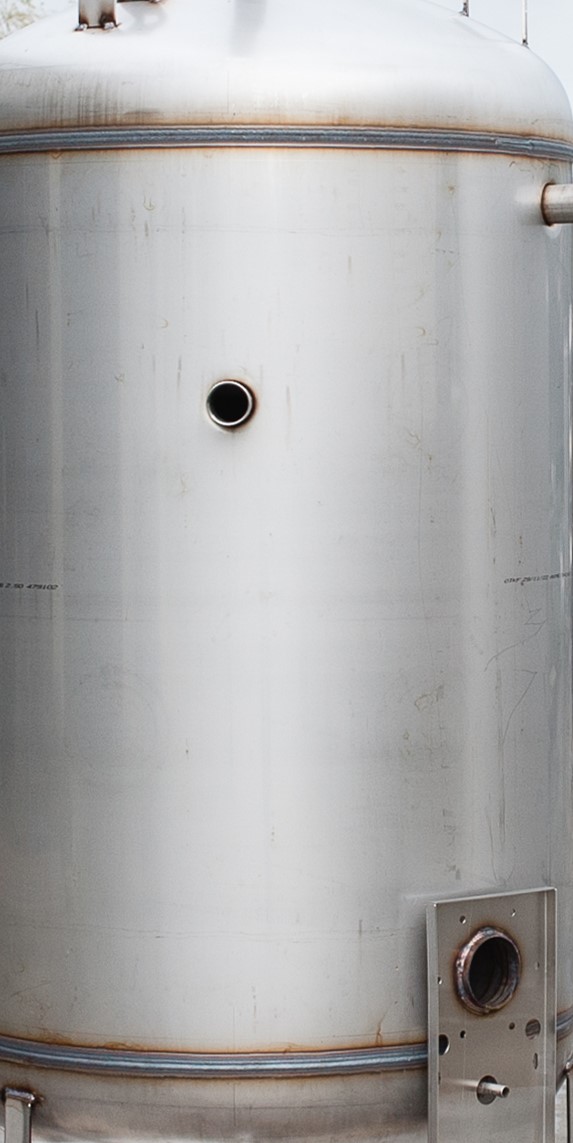
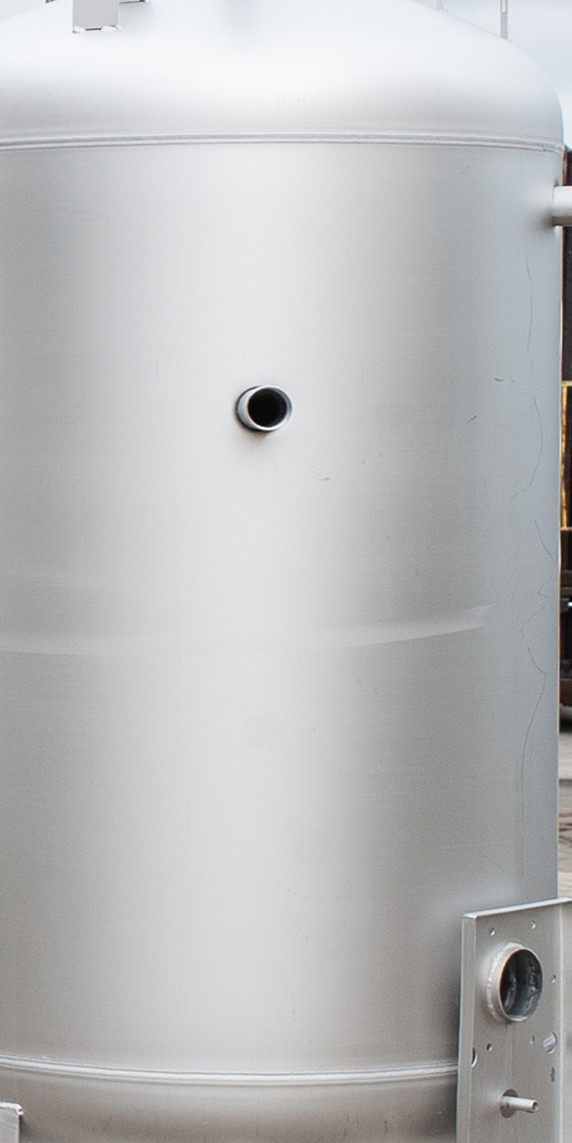
Electropolishing

Electropolishing is an electrochemical process that “dissolves” the layer surface of a metal. The part to be treated is immersed in an acid electrolyte bath and is connected to the anodic pole. Under the application of a direct current, there is dissolution of the metal to be treated and release of oxygen at the cathode. The dissolution phenomenon is directed preferentially on micro-asperities. Thus, the surface is leveled and becomes shiny, this process is called electropolishing.
It is this last technique that was chosen in order to make the new stainless steel exterior skin of the Atomium shine.
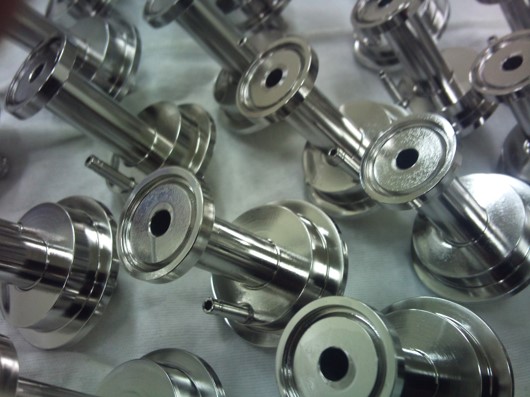
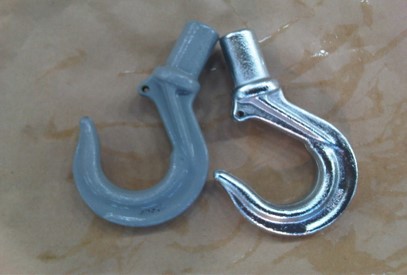
Interested in our Workshop services?
Derouging

Chimiderouil, through its experience in the field of stainless steel and the continuous development of new product formulations, can help you solve the rouging problems that you encounter in your installations.
Stainless steel installation rouging is the result of the formation of iron oxide, hydroxide or carbonate from an external source or linked to the destruction of the passive layer of the stainless steel. The color variation is linked to the type of oxide formed and variation in the water associated with the corrosion process.
Colors vary from orange to black. A high-performance team will offer you a diagnosis and solutions adapted to your needs.
Before
After
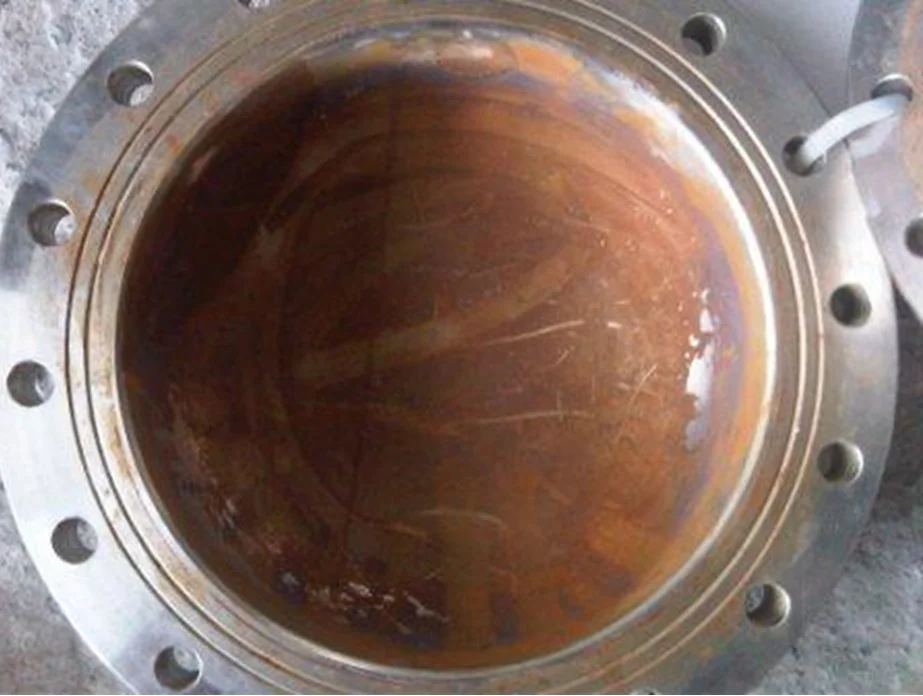
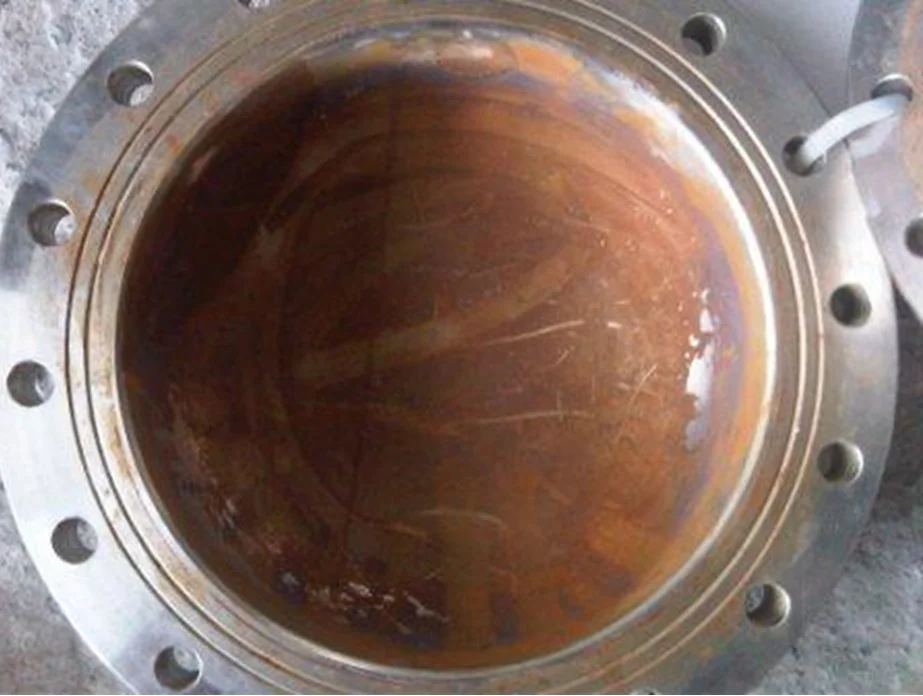
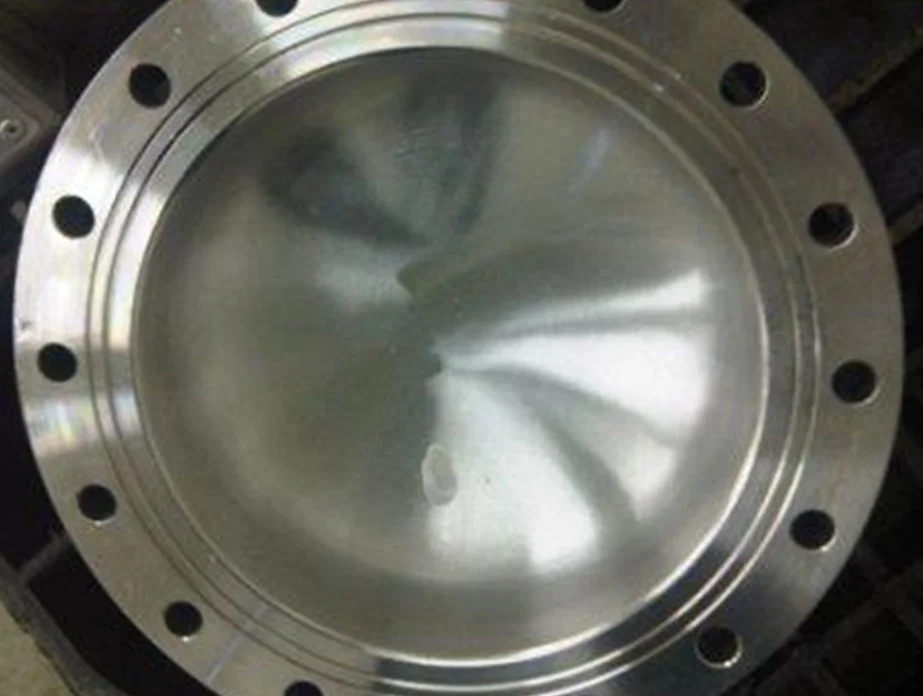
Oxygen degreasing

Oxygen service essentially requires the complete removal of contaminants such as
- greases
- hydrocarbons
- oils
- thread lubricants
- impurities due to work
- polluted water
- filings
- scale
- weld projection
- shavings
- paints
- varnish
- pencil marks
- rust
- oxides
- powdered metals
- packaging material
- labels
- wood fiber
or any other foreign material
Before
After
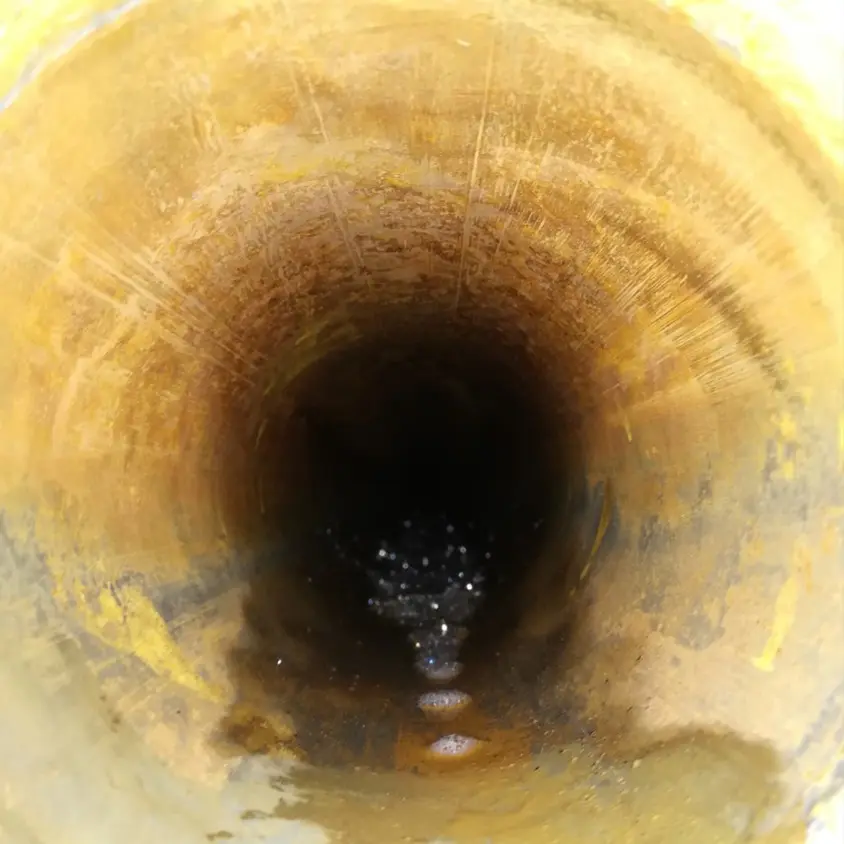
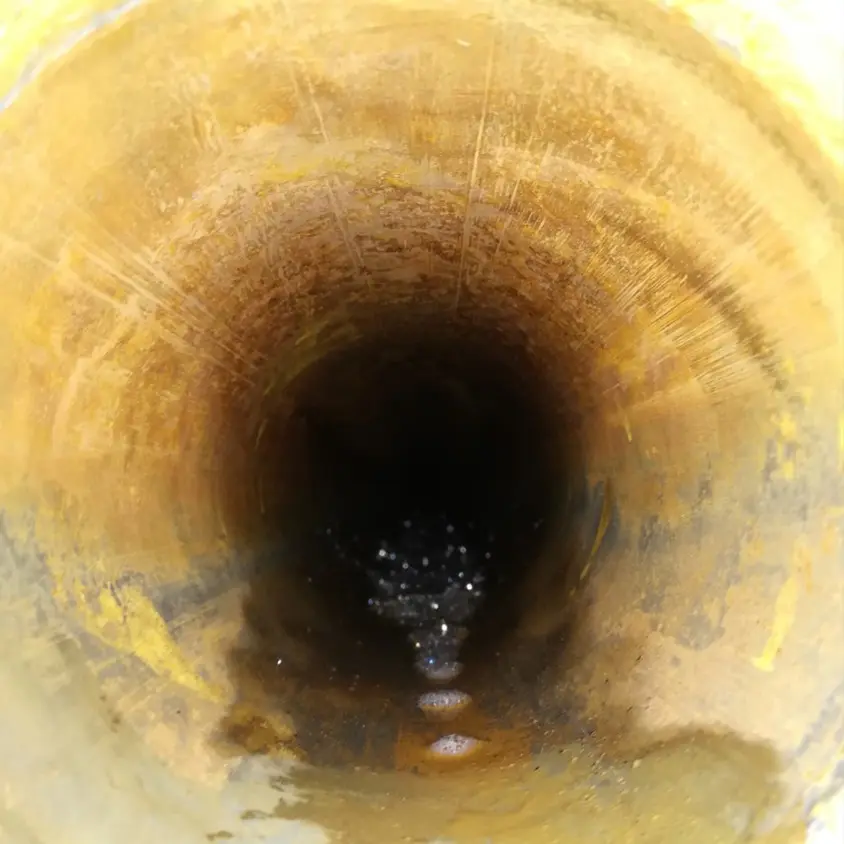
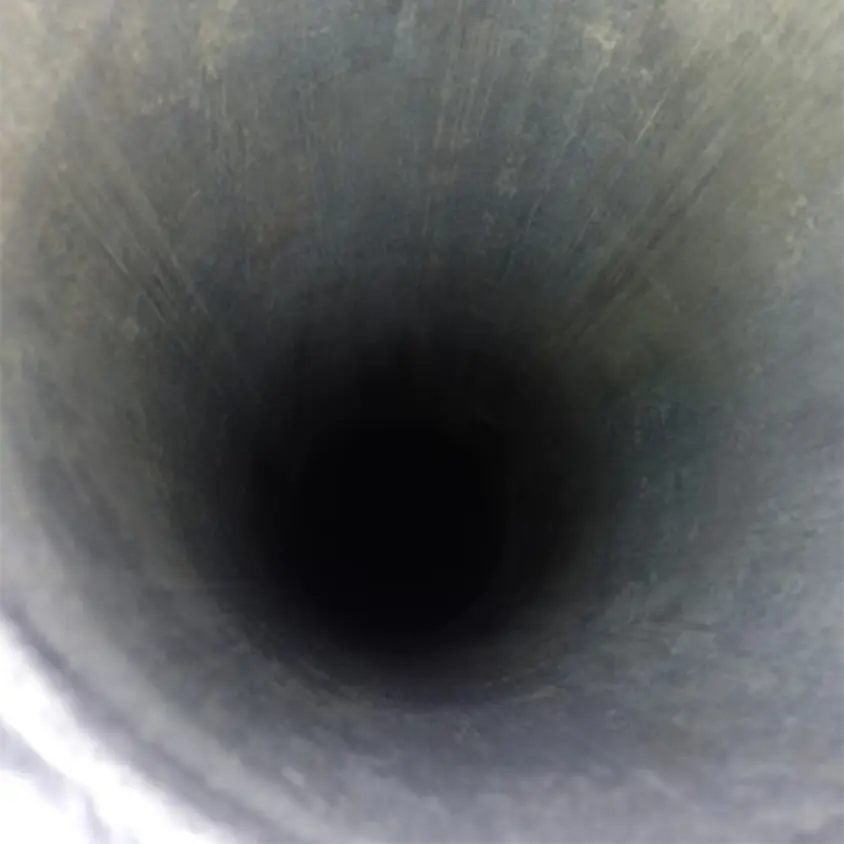
Many of these materials, especially greases, more or less oxidized metal powder, hydrocarbons and oils can react violently in the presence of oxygen, causing fires and explosions. Others, such as metal shavings, can be propelled by a fluid circuit with sufficient speed to trigger an explosion on impact.
Chimiderouil offers the appropriate chemical treatments to prepare your installation, your pipes or exchangers for this type of specific application. We have the appropriate chemical formulations for each grade of steel and offer the appropriate means of control (Wood’s lamp, water film test, etc.). Our working methods correspond to the requirements of the Eiga IGC Doc 33/06/E standard.
Descaling

Chimiderouil can help you solve your scaling problem, both from a preventive and curative point of view. Our teams take charge of managing the treatment of your installations, thus ensuring optimal performance of your installations!
Why descaling your exchangers and boilers There are two main reasons for descaling your exchanger.
On the one hand, the presence of scale will lead to excess energy consumption to ensure the proper functioning of the device, which will undeniably be felt on your energy bill: 1mm of scale deposited = 15% energy lost.
On the other hand, the scale deposit will adversely affect the proper functioning of the exchanger or boiler by increasing the risk of corrosion and reducing its lifespan.
Our long experience allows us to select the appropriate chemistry to solve your problems. Do not hesitate to contact our engineers to help you in your specific cases!
Before
After
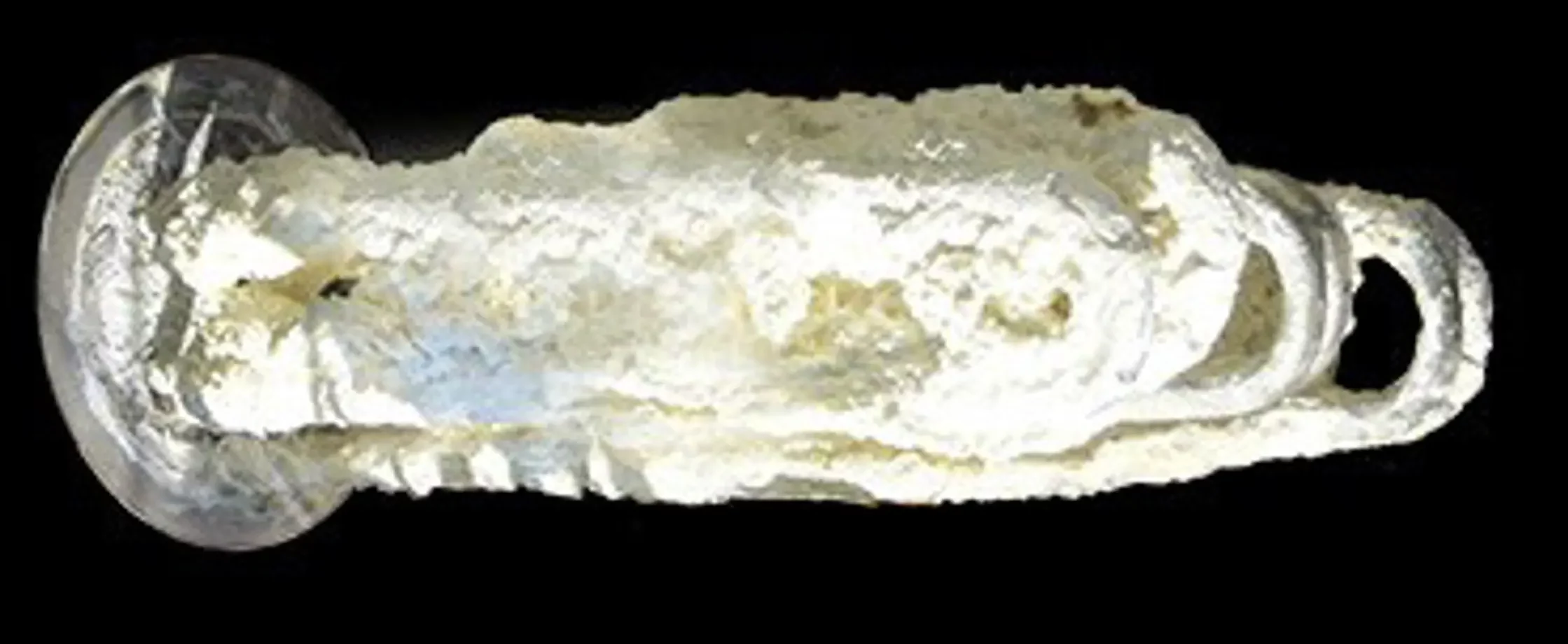
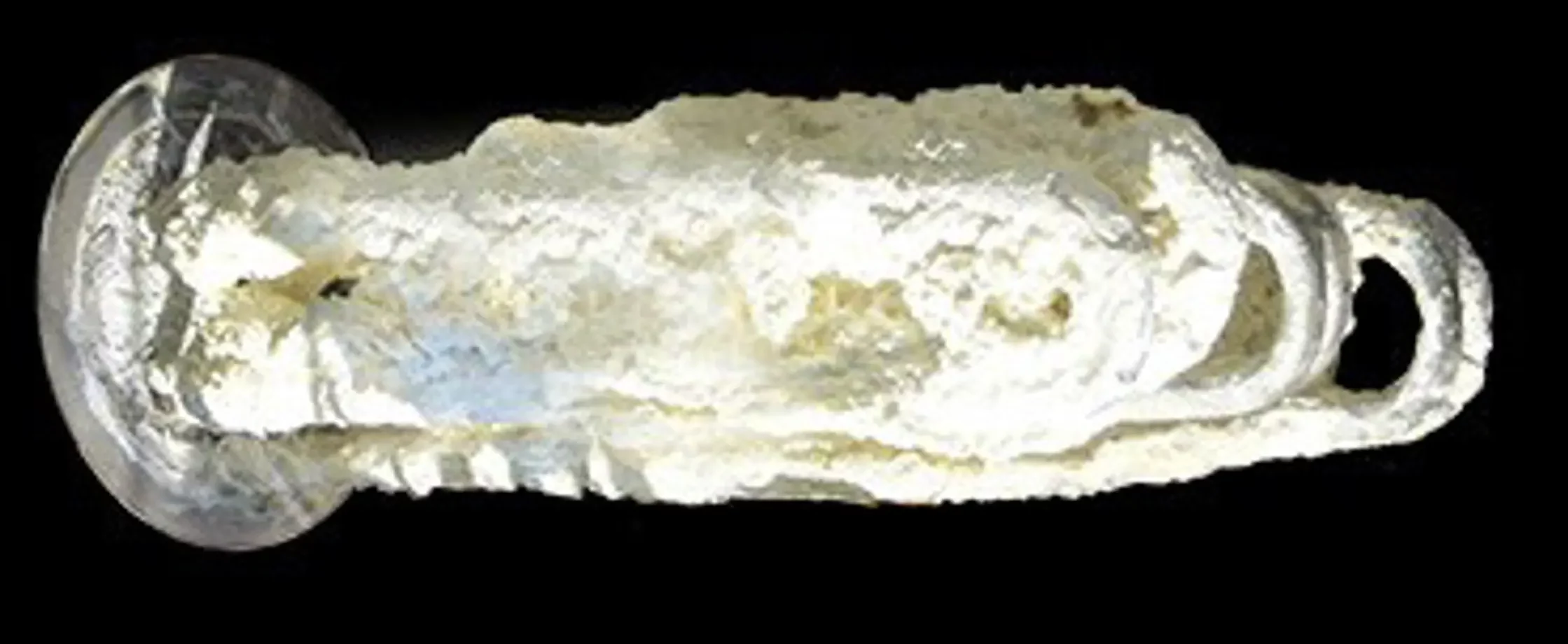
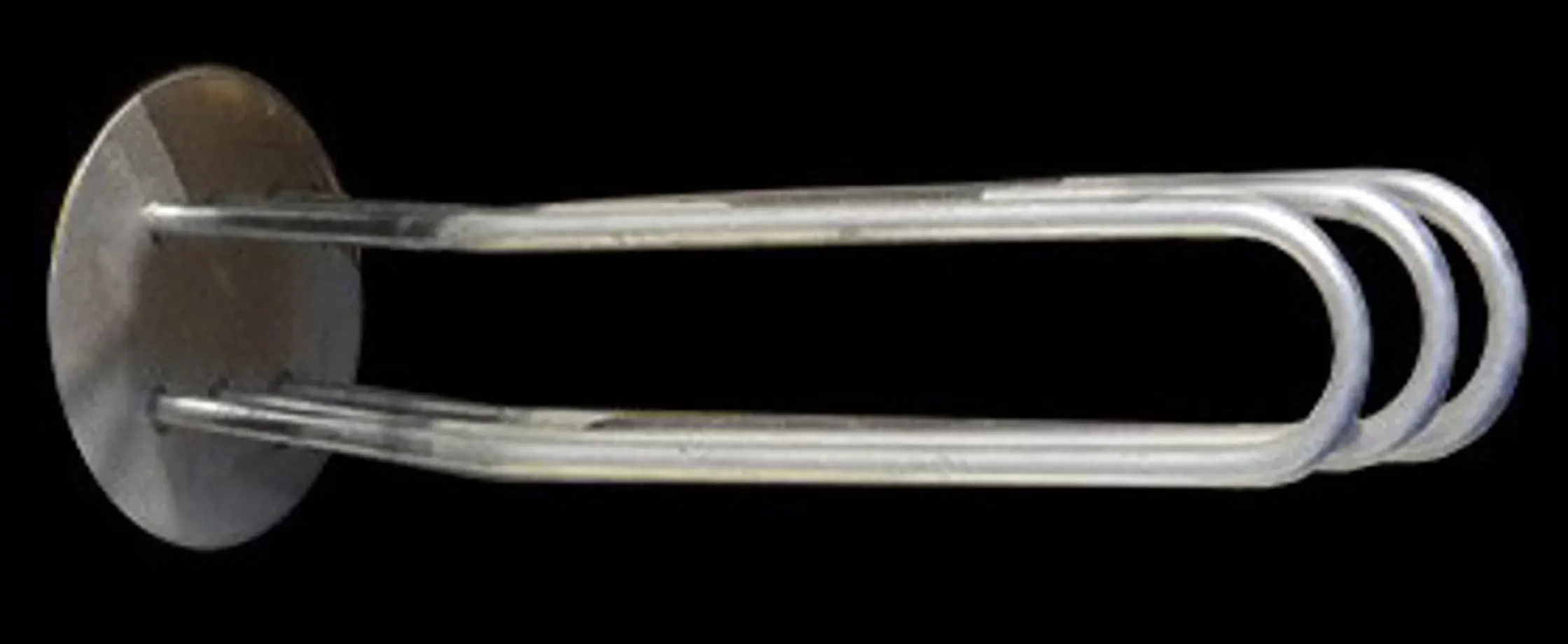
Chemilling

“Chemilling”, an abbreviation of chemical milling, is the English term for “chemical machining”. The objective is to homogeneously and precisely remove a thickness of material from a part of complex geometry. This is done by attacking the metal with a chemical solution.
In the case of Chimiderouil, we practice this process on titanium parts. The objective of the treatment is either to improve the roughness of the part, or to dissolve the alpha-case which may have formed during the casting of the part.
Chimiderouil is Nadcap certified for these operations and is also qualified by operators such as Airbus, Safran... With the latest developments in terms of additive manufacturing, Chimiderouil has also adapted this process in order to improve the surface condition of titanium parts produced using additive manufacturing.
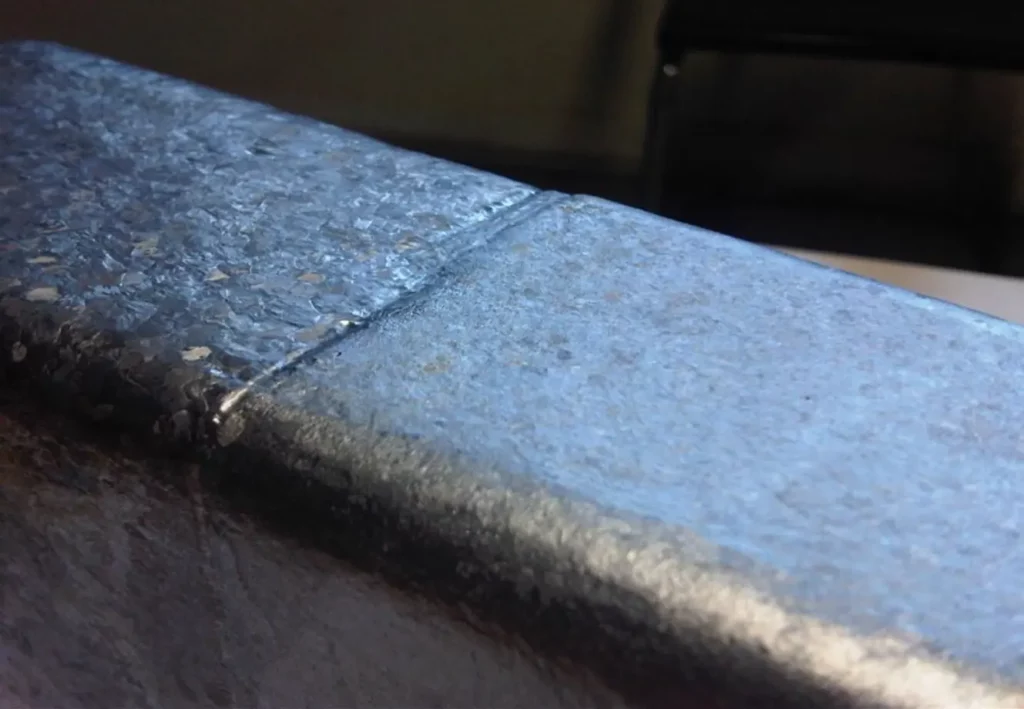